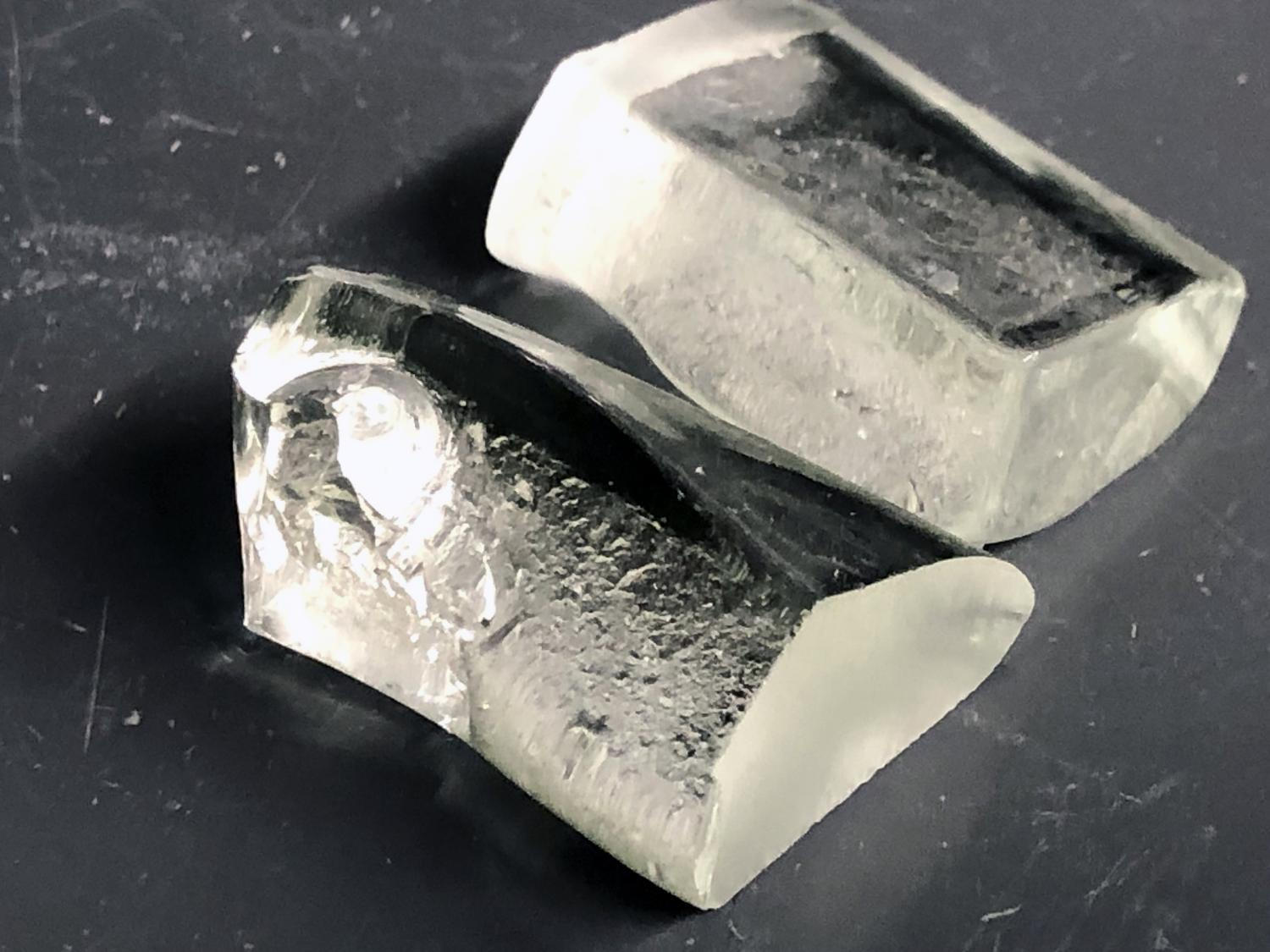
A sample of LionGlass, a new type of glass designed by researchers at Penn State that requires much less energy to produce and is more resistant to damage than standard soda-lime silicate glass. Credit: Adrian Berard/Penn State
Globally, glass manufacturing results in the least 86 million tons of carbon dioxide annually. However, a new type of glass called LionGlass, developed by Penn State researchers, offers the potential to reduce this carbon output by 50%. Not only does this innovative glass require much less energy to produce, but it also has greater damage resistance than traditional soda-lime silicate glass. The scientists behind this breakthrough recently filed a patent application, marking the initial step toward bringing LionGlass to market.
“Our goal is to make glass manufacturing sustainable over the long term,” said John Mauro, the Dorothy Butt Enright Professor of Materials Science and Engineering at Penn State and principal investigator on the project. “LionGlass reduces the use of carbon-containing batch materials and greatly lowers the melting temperature of glass.”
Soda-lime silicate glass, the common glass used in everyday items from windows to glass tableware, is made by melting three basic materials: quartz sand, soda ash, and limestone. Soda ash is sodium carbonate and limestone is calcium carbonate, and both release carbon dioxide (CO2), a greenhouse gas that traps heat, as they melt.
“During the glass melting process, the carbonates decompose into oxides and produce carbon dioxide, which is released into the atmosphere,” Mauro said.
But the bulk of the carbon dioxide emissions come from the energy needed to heat the kilns to the high temperatures needed to melt glass. With LionGlass, melting temperatures drop by about 300 to 400 degrees CelsiusMauro explained that this leads to a reduction in energy consumption of approximately 30% compared to a traditional soda-lime glass.
Not only is LionGlass easier on the environment, it’s also stronger than traditional glass. The researchers said they were surprised to find that the new glass, named after the Nittany Lion’s mascot in Pennsylvania, had higher crack resistance than conventional glass.
Certain glass panel fixtures have such strong crack resistance that the glass will not crack, even under a force load of one kilogram of Vickers diamond pipe. LionGlass is at least ten times more crack resistant than standard soda-lime glass, which forms cracks under a load of about 0.1 kilograms of force. The researchers explained that LionGlass’s limits had not yet been found, because it had reached the maximum load that the indentation equipment would allow.
“We kept increasing the weight on LionGlass until we reached the maximum load that the equipment would allow,” said Nick Clark, a postdoctoral fellow in Mauro’s lab. “It simply won’t break.”
Mauro explained that crack resistance is one of the most important qualities to test in glass because this is how the material ultimately fails. Over time, the glass develops small cracks along the surface, which become weak points. When a piece of glass breaks, it is due to the weaknesses caused by the microcracks that are present. He added that glass that is resistant to the formation of microcracks in the first place is of particular value.
“Damage resistance is a particularly important property of glass,” said Mauro. “Think of all the ways we rely on the strength of glass, in the automotive and electronics industries, in architecture, and in communications technology like fiber optic cables. Even in healthcare, vaccines are stored in strong, chemically resistant glass containers.”
Mauro hopes that LionGlass’ improved strength means that products created from it can be even lighter. Because LionGlass is ten times more resistant to damage than current glass, it can be significantly thinner.
“We have to be able to reduce the thickness and have the same level of damage resistance,” said Mauro. “If we have a lighter product, it’s better for the environment, because we use less raw materials and we need less energy to produce it. Even downstream, for transportation, it reduces the energy needed to move the glass, so it’s a win-win situation.”
Mauro notes that the research team is still assessing LionGlass’ potential. They have filed a patent application for the entire glass family, which means there are many compositions within the LionGlass family, each with its own distinct characteristics and potential applications. They are now exposing different formulations of LionGlass to a range of chemical environments to study how they interact. The findings will help the team develop a better understanding of how LionGlass is used around the world.
“Humans learned how to make glass more than 5,000 years ago, and since then it has become imperative to bring modern civilization to where it is today,” Mauro said. “Now, we are at a time when we need to help shape the future, as we face global challenges such as environmental issues, renewable energy, energy efficiency, healthcare, and urban development. Glass can play a vital role in solving these problems, and we are ready to contribute.”
“Explorer. Unapologetic entrepreneur. Alcohol fanatic. Certified writer. Wannabe tv evangelist. Twitter fanatic. Student. Web scholar. Travel buff.”